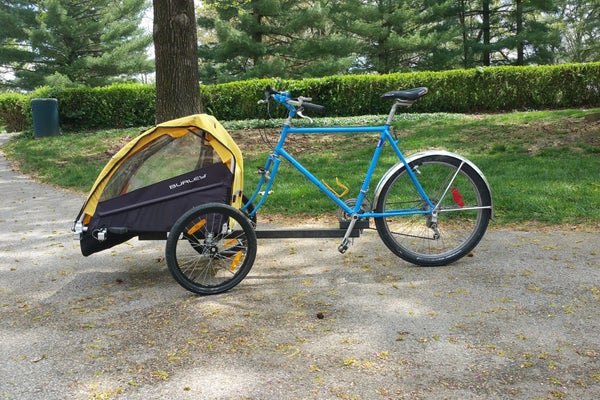
Le marché du vélocargo se porte bien aujourd’hui. On le constate en observant des triporteurs même dans des petites villes, comme Laval, où l’idéologie de la bagnole n’est pas nécessairement plus tenace qu’ailleurs, mais où les conditions matériels de l’aménagement routier et de l’urbanisme n’invitent guère aux déplacements doux. Le triporteur a une capacité de charge conséquente, proche de celle de l’automobile citadine, et une motricité musculaire (éventuellement assistée par EDF, mais à hauteur de 60 à 250 Watts, contre quelques 10 à 20 000 Wh pour une voiture en ville 1). Il combine donc l’avantage du vélo et de la voiture, quand il s’agit d’aller chercher quelqu’un ou de faire des courses volumineuses.
Le vélocargo, oui, mais…
On ne va pas dédier cet article intégralement à l’éloge du vélocargo. Des centaines de pages existent déjà en ligne pour ce faire. Il y a par contre des bémols au vélocargo, qu’on n’aborde pas toujours dans ces mêmes pages :
- C’est cher. Souvent quelques milliers d’euros, rarement moins de 1500-2000 euros. On peut toujours relativiser, considérer qu’un vélocargo qui remplace une voiture est vite amorti, avec l’assurance, l’essence en moins. Mais pour un ménage urbain ou péri-urbain, si ses revenus sont modestes, un tel prix pour un véhicule encore peu familier est souvent rédhibitoire.
- C’est encombrant. Si vous avez de la place, un garage, tant mieux. Peu de gens laissent stationné dehors et de nuit leur vélocargo. Encore inhabituel, coûteux et plus facile à voler (à l’aide d’un camion ou d’une meuleuse) qu »une voiture, ou trop aimés pour être exposé au soleil et à la pluie ? Je ne saurai dire les motivations premières de leurs usagers, mais j’observe peu de vélocargos stationnés dehors la nuit. Même pour ceux ayant un garage, avoir dedans à la fois le vélo et le vélocargo est un encombrement supplémentaire. Je suppose que vous voyez ou je veux venir…
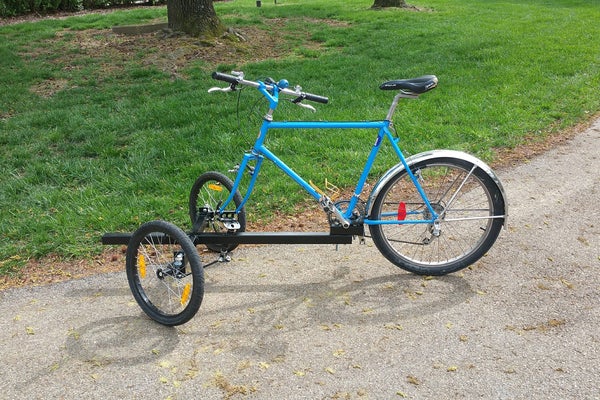
Détachable, pliable, téléscopique, solaire, quand seule l’imagination peut nous limiter
Pour ces raisons il me semble pertinent d’envisager le problème autrement. Si le problème du vélo est sa capacité de charge limitée, pourquoi acquérir un autre véhicule que de la lui donner ? Pourquoi ne pas permettre au vélo qu’il soit tantôt un outil de locomotion rapide et léger, frêle et passe-partout, tantôt un triporteur certes moins versatile mais avec tout ce qu’il peut porter ? On gagne ainsi sur les deux tableaux des inconvénients cités : moins cher, puisque cela ne requiert que la fabrication du train avant et de la caisse, sans le vélo derrière, qui ne serait qu’un doublon de notre destrier habituel, triste jaloux oublié au garage. Moins encombrant, on démonte le châssis du cargo, et si possible on replie la caisse.
Pour que ce concept soit valable, il faut que ce soit simple et ergonomique. Dans l’idéal le châssis monté ou démonté en une ou deux minutes, la caisse plié en pas plus de temps. Il faut évidemment aussi que la sécurité soit là, avec une résistance éprouvée du chassis et du train avant, une géométrie propre et stable de ce dernier notamment dans les virages, et un système de freinage proportionné au poids potentiellement propulsé.
Des modèles et sources d’inspiration existent déjà, outre-atlantique, un modèle commercial pour un biporteur, comme un modèle fait maison de triporteur. Les deux existent déjà, et transmettent l’envie de fair encore mieux. Le mécanisme à chaque fois employé est le même : Deux attaches, une sous le pdélier ou derrière lui, une autre sur la fourche avant. On enlève la roue avant, puis on pose le vélo sur le châssis du module. Un coup de boulon entre l’attache préfixée au niveau du pédalier, la fourche avant glissée dans un axe perpandiculaire à l’axe de direction à une distance préréglée et modifiable de ce dernier. L’axe de direction se prolonge ainsi par une potence qui passe à travers le tube principal du châssis, et trasnmet la direction en dessous de celui-ci aux roues. La fourche avant et cette potence modifiée servent ainsi à la fois de support du vélo et à transmettre la direction, comme sur un vélo normal en fin de compte.
De là, l’imagination et la patience sont presque les seules limites. Si le châssis doit bien répondre à certaines contraintes de solidité et de géométrie, tout ce qui est au dessus peut se décliner de pultiples façons. On peut imaginer y mettre un caisson pliable et/ou lui même amovible, pour un encombrement réduit à l’extrême du module une fois rangé. Les mateurs de vitesse pourront préférer sacrifier une partie de leur capacité de charge à un système de train avant à bascule, pour se pencher dans les virages presque autant que sur une bicyclette. Les cyclovoyageurs préfereront une caisse téléscopique pour en faire un couchage rapidement déployé, avec un panneau photovoltaïque pour couvrir la caisse tout en permettant de rechargeant leur batterie, pour une autonomie accure. Les artisans seraient satisfaits d’une caisse adaptée à leurs outils, facilement démontable ou déployable.
Les avantages d’une telle modularité on le voit sont multiples. C’est celle-ci qui donne au module le potentiel de prise en main, d’autonomie et de convivialité dans la mobilité, potentiel auquel on a tous le droit d’aspirer.